Preparation for ISO 9001 certification
With the ISO 9001 certification, companies can prove that they have implemented quality processes when creating products or providing services. These quality-oriented processes extend to all areas of the company (e.g. purchasing, human resources, sales, logistics). The process landscape therefore plays an important role on the path to successful certification according to ISO 9001. The representation of the process landscape is only part of the documents for the certification of the quality management manual. A quality management system (QMS) requires a variety of documents for ISO 9001 certification. These QM documents must be adapted to the business processes, risks and requirements of the respective company. As soon as all documents are complete, the ISO 9001 preparation for the audit begins. The ISO IEC 9001:2015 standard requires training of all employees to improve quality awareness (e.g., “QM Training”).
For the ISO9001 audit date, you need standard-compliant documents, with all the necessary evidence, process documentation and implementation protocols. A nice document folder with a run-of-the-mill set of rules will not pass the audit. Anyone who does not implement the technical or human resources for quality assurance will have significant deviations certified in the external audit. Although auditors largely examine the documents presented, technical aspects may be addressed in the first audit or in subsequent control audits. If the auditor determines that it is just a management system that has not been implemented, he may be forced to declare the certificate that has already been issued invalid.
We have provided a short video for you here on the subject of audit preparation:
What kind of evidence do you need for an ISO 9001 audit?
As you could already see from the video, you definitely need the following to carry out a qualitative ISO9001 audit:
- Individualized management system according to ISO/IEC 9001 (in DOCx or PDF format)
- Representation of the process landscape
- Proof of the appointment of a QM representative
The following documents, measures and evidence may also be required:
- Visualization of individual process flows
- Template folder with various forms
- Documentation of the process optimizations made, e.g.
- Change reports & notes in the QM manual
The list above shows that you should be well prepared for the QMS audit. Not all of the measures recommended above need to be taken. The more of these are implemented, the better able you are to live by the required set of rules. We not only help you quickly put together the extensive set of rules, but also take any necessary measures and receive the absolutely necessary training.
What are the requirements for a certifiable QMS according to ISO 9001?
In addition to the main document (referred to as the QM manual), the quality management system must also contain a number of forms and relevant operational attachments. Preparation for ISO 9001 certification must ensure that a complete quality management manual with all process descriptions is in place. Process visualization is not absolutely necessary, but it makes it easier for the QM representative and the ISO9001 auditor to understand the process flows described. The requirements of the ISO9001 standard and the accreditation bodies lead to the following important core requirements:
- Process documentation as an ISO 9001 requirement
- Quality management planning and documentation
- Internal audits are an ISO 9001 certification requirement
- Quality policy and binding quality goals
Even if you are convinced to be ready for the audit, spend time to go over the ISO 9001 checklist. You might have forgotten a vital aspect after having draften many documents.
How strictly do auditors check the ISO9001 QMS?
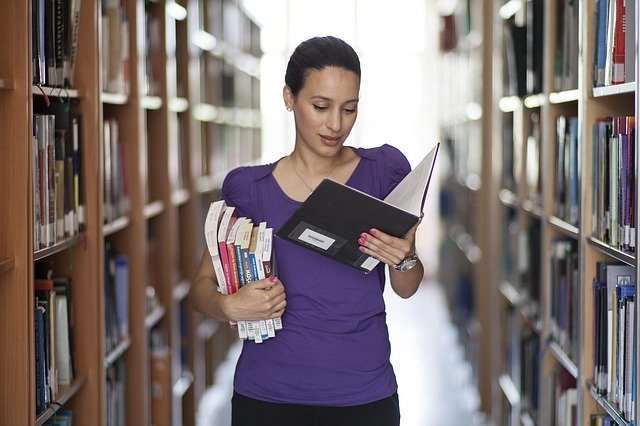
First, the auditors check the completeness of the documents and the plausibility of the information provided there. Then they specifically focus on individual critical points as well as noticeable components. For SMEs, the management system consists of a manageable number of documents. This helps the auditor save a lot of time. Nevertheless, he is also required to take samples that he knows from his “auditing practice” to be aspects that are mostly neglected or often missing. It would be highly recommended to have at least some documents to hand. This information convinces the auditor that all processes follow the predetermined sequence of steps.
Frequently asked questions about preparing for ISO9001 certification
The company determines all processes needed to “meet the requirements for the provision of products and services”. These core and support processes must be systematically documented and managed.
The type of documentation is not specified in the ISO 9001 requirement. The documentation simply has to be suitable for operational planning and control in its respective form. The process documentation should show the process flow (“what is being done”). The details of the implementation do not have to be specified in the QM manual. A reference to a separate document can be entered. This makes documentation maintenance easier. All process-relevant information about the process and measurement using key figures should already be documented in the first level of the process documentation.
A quality management plan must be set up: It contains the management's declaration of commitment to comply with the quality policy and specifications, as well as to ensure the processes. The documentation includes an audit plan for internal audits. The resulting measures must be recorded and their implementation recorded. Opportunities and risks should be discussed with management at regular intervals.
Auditors from the certification bodies check the documentation from past internal audits. Internal audits promote improvements and the detection of planning errors. This means that any process errors caused can be identified at an early stage. The results of the internal audit show where there is potential for improvement in the organization. In addition, employees are sensitized to the topic of quality management.
Management must specify an individual and suitable QM policy.
The quality policy must be appropriately defined for the purpose of the organization and its business context. It should serve as a framework for quality objectives and contain a commitment to continuous improvement. A good quality policy is based on the mission and vision of the company. It is the basis for high-quality service or production. This makes the quality policy part of the company philosophy. The company philosophy places quality and customer satisfaction at the highest priority.
Quality goals are based on the company's quality policy. Responsible people are assigned to the goals. The goals are measurable using a target date and an indicator for measuring goal achievement. The assessment of target achievement is incorporated directly into the annual management review.
Quality assurance refers to the following characteristics as acceptance criteria: characteristics of the products, services or activities that are crucial for quality.