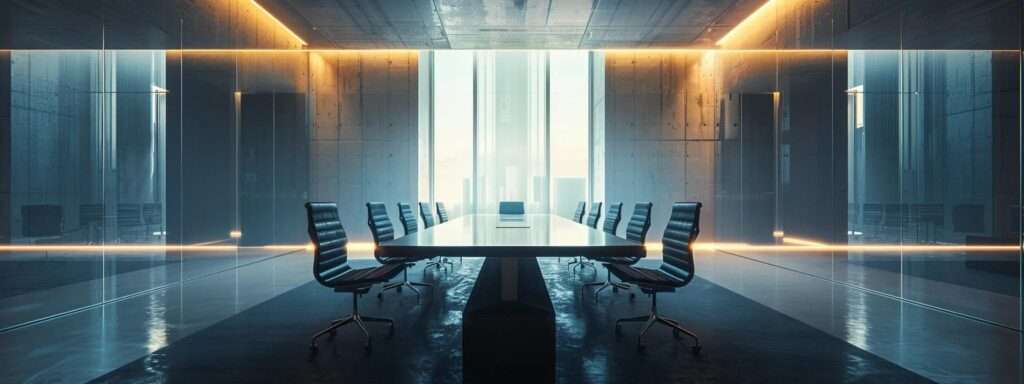
ISO 9001 Quality Manual Examples for Effective Implementation
In today’s competitive business landscape, achieving ISO 9001 certification is not merely a regulatory necessity but a strategic advantage for organisations seeking long-term success. A robust Quality Management System (QMS) not only fosters continuous improvement but also builds trust with customers, stakeholders, and regulatory bodies. By adopting
and best practices, companies can ensure conformity, manage risk effectively, and deliver consistent quality across all processes. This article outlines practical examples of ISO 9001 Quality Manuals and explains how these documents serve as the foundation for a successful QMS. It discusses the purpose, structure, core components, implementation strategies, certification alignment, and continuous improvement measures represented in well-crafted quality manuals. Key elements such as six sigma principles, conformity assurance, quality control checklists, and communication protocols are embedded throughout the manual. The objective is to provide IT directors, business leaders, and founders with actionable insights into developing, implementing, and refining a Quality Management System that supports audit readiness, effective leadership, and organisational excellence.Transitioning from a conceptual QMS to tangible best practices requires systematic documentation. The following sections delve into each aspect of the streamlined process, offering step-by-step guidance and real-world examples for enhancing operational performance and securing certification.
Defining the Purpose and Scope of Your QMS Through the Quality Manual
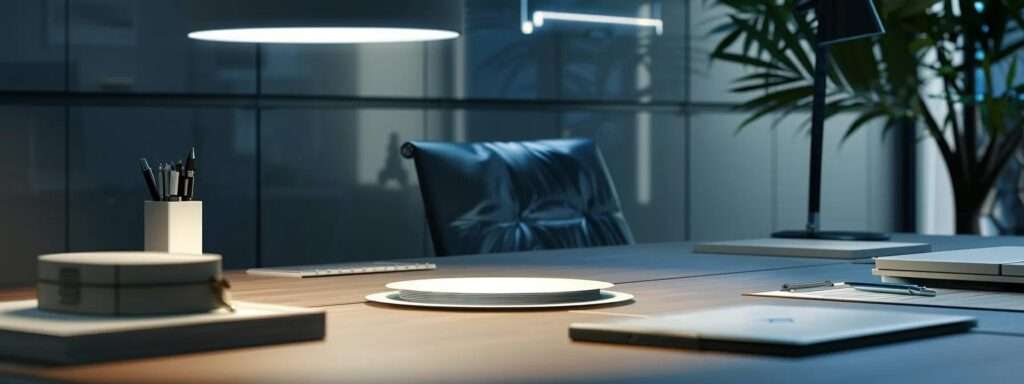
Developing a Quality Management System (QMS) begins with a clear understanding of its purpose and scope, as explained within the Quality Manual. The manual serves as a blueprint for all quality-related activities, ensuring that every process contributes to the overall goals of the organisation. It details the strategic objectives, operational boundaries, and the roles that various stakeholders play in maintaining and improving quality standards. By clearly defining the manual’s intent, organisations can ensure that all procedures align with both internal expectations and requirements, thereby facilitating audits, risk management, and certification processes.
Articulating Your Organisation's Context Within the Quality Manual
The Quality Manual must reflect an honest and comprehensive analysis of the organisation’s internal and external context. This includes an assessment of market expectations, regulatory requirements, and the operational environment. The document should detail how organisational culture, strategic direction, and stakeholder demands influence quality objectives. For instance, companies operating in highly regulated industries often embed regulatory compliance measures and risk assessments directly into their quality documentation. This articulation not only improves the clarity of the Quality Management System but also aids auditors in understanding the organisation’s unique challenges, ensuring that the manual remains a living document that adapts to changing business scenarios.
Establishing Clear Quality Objectives Within Your Manual
Quality objectives form the backbone of the QMS by defining what the organisation aims to achieve. These objectives need to be specific, measurable, achievable, relevant, and time-bound (SMART). The Quality Manual should articulate goals such as improving delivery lead times by a defined percentage, reducing errors in production, or enhancing customer satisfaction scores. Clearly laid-out objectives help in aligning the team’s efforts, ensuring accountability, and providing a clear framework for evaluating performance. In organisations where six sigma techniques are applied, the manual might include precise targets related to defect reduction and process optimisation, which further underpins the QMS with its quality objectives.
Detailing the Scope of Your Quality Management System
An essential element of the Quality Manual is a precise delineation of the QMS scope. This section should outline which processes, departments, or product lines are covered by the QMS. By clearly defining the boundaries, companies avoid ambiguity during audits and facilitate a targeted performance assessment. The scope statement typically describes the operational limits and any exclusions that have been justified due to the nature of specific processes or regulatory requirements. For example, a manufacturing firm may exclude certain purely administrative functions that do not impact product quality, provided there is documented evidence supporting such a decision. Such detailing ensures that every aspect of the quality system is accounted for, reducing risk and enhancing operational efficiency.
Referencing Key Processes and Their Interactions for QMS Success
A functioning QMS relies on the seamless integration of various processes. The manual must map out these interactions, demonstrating how each process supports quality objectives. This includes linking supplier management, production, customer feedback, and continuous improvement initiatives. The document may contain flowcharts or process maps that visually represent these interactions, ensuring that users understand the interdependencies. For example, an effective manual might detail how corrective actions initiated from audit findings feed back into the process improvement cycle through PDCA (Plan-Do-Check-Act) methodology. Such referencing not only clarifies operational workflows but also fosters organisational learning by highlighting areas that require ongoing optimisation.
How the Manual Underpins Successful QMS Implementation Efforts
Ultimately, the Quality Manual is the cornerstone of a successful QMS implementation. It is not merely an administrative record, but a dynamic tool used for training, risk management, and performance monitoring. A well-crafted manual aligns with ISO 9001 requirements and supports internal audits by providing clear evidence of compliance, accountability, and continuous improvement. Organisations often use templates derived from industry best practices and modify these examples to fit specific business needs. This alignment ensures that when the time comes for certification audits, all evidentiary documents and processes are readily accessible and reflect actual practices. By integrating six sigma principles, PDCA cycle, and risk-based thinking, the manual becomes an essential reference point for sustaining quality, controlling risk, and driving long-term operational success.
Structuring Your ISO 9001 Quality Manual for Optimal Use and Compliance
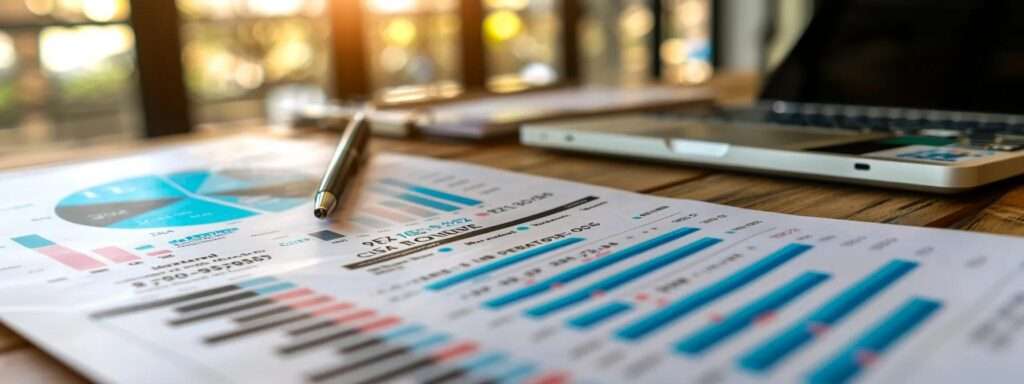
A well-structured ISO 9001 Quality Manual is crucial for achieving compliance and ensuring that the QMS is user-friendly and effective. The structure must facilitate easy navigation, clear documentation, and regular updates. A logical document structure is indispensable for managing complexity and ensuring that every element—from policy statements to detailed work instructions—contributes to the system’s overall efficiency. By adopting a framework that mirrors the ISO 9001 clauses, organisations can align their internal practices with international standards seamlessly.
Selecting an Appropriate Format for Your Quality Manual Documentation
When choosing a format for the Quality Manual, organisations should consider both operational needs and audit compliance. The format, whether digital or physical, must be accessible to everyone within the organisation. A common approach is to use a digital document management system that offers version control, searchability, and secure access. This is particularly important in modern organisations where remote work and decentralised teams are prevalent. By utilising compliant templates, companies can standardise the layout, ensuring that each section adheres to a consistent visual hierarchy. Such a format also simplifies future revisions, ensuring that the manual remains current amidst rapid changes in business practices and regulatory environments.
Organising Content Logically Around ISO 9001 Clauses
To promote clarity and compliance, the Quality Manual should be organised in a manner that reflects the structure of the standard. Each section of the manual should correspond to specific clauses of the standard, from context of the organisation to performance evaluation and continual improvement. By mapping content to these clauses, users can quickly locate information pertinent to audit requirements or operational excellence. This logical organization also aids in training new employees, as it provides a clear roadmap of how quality processes interrelate and contribute to overarching business goals. For instance, the section on “Risk-Based Thinking” might begin with an introduction to the PDCA cycle, then move into detailed processes and performance metrics, linking back to ISO requirements consistently.
Ensuring Easy Navigation and Accessibility for All Users
Ease of navigation is a critical component of an effective Quality Manual. All sections must be easily accessible and searchable to support daily operations and audits. Hyperlinked tables of contents, clear headings, and cross-references between related sections can significantly enhance usability. The manual should serve as a handy reference tool not only during audits but also during training sessions and process reviews. This feature is especially important for large multinational organisations where employees from diverse backgrounds and technical proficiencies rely on clear, straightforward documentation to perform quality-related tasks efficiently.
Incorporating Version Control and Document Management Principles
A dynamic Quality Manual requires stringent document management practices, including version control. As operational procedures and regulatory requirements evolve, the manual must be updated systematically. Version control ensures that all changes are documented, approved, and communicated to relevant personnel. This process reduces the risk of outdated information being used during audits or internal reviews. Adopting a robust document management system, which may include cloud-based repositories and electronic signatures, helps maintain a historical record of manual revisions. This traceability is not only a best practice in quality management but also a requirement for ISO 9001 certification, as it demonstrates ongoing commitment to continuous improvement and compliance.
Reviewing ISO 9001 Quality Manual Examples for Structural Insights
Many organisations benefit from reviewing exemplar industry templates to gain structural and content-related insights. These examples provide practical guidelines on how to document procedures, assign responsibilities, and integrate continuous improvement elements. Case studies from industry leaders often highlight best practices, such as aligning quality objectives with strategic business goals and incorporating regular feedback mechanisms. In these examples, quality manuals often include detailed flowcharts, checklists, and performance metrics that demonstrate how quality is measured and managed across the organisation. By benchmarking against these examples, companies can adapt proven strategies to meet their specific business needs and ensure that their manuals are both comprehensive and compliant.
Core Components and Content From ISO 9001 Quality Manual Examples
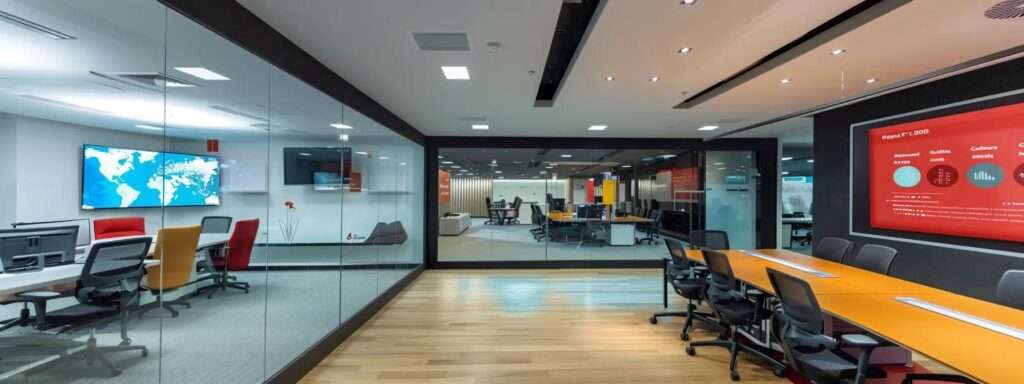
The core components of a Quality Manual are the building blocks that ensure the Quality Management System is effective and compliant with industry standards. These components range from strategic elements, like the Quality Policy, to operational details such as documented procedures and work instructions. Understanding the essential content required in a Quality Manual enables organisations to build a robust framework that drives quality, manages risk, and supports scientific methodologies like PDCA and six sigma practices.
Documenting Your Quality Policy and Communicating It Effectively
One of the first and most critical components of the Quality Manual is the Quality Policy. This statement articulates the organisation’s commitment to quality and continuous improvement. It must be concise yet comprehensive, reflecting both the organisation’s strategic vision and operational goals. The Quality Policy should be communicated effectively across all levels of the organisation, ensuring that every employee understands how their role contributes to overall quality objectives. In many examples, organisations use clear, measurable targets within their policy, which helps align individual performance with corporate goals. Furthermore, the policy often serves as a reference point during internal audits and management reviews, confirming that quality is embedded in the company’s culture.
Outlining Roles, Responsibilities, and Authorities Within the QMS
A robust Quality Manual delineates the roles, responsibilities, and authorities of all personnel involved in the QMS. This includes senior management, quality managers, operational staff, and even external stakeholders such as suppliers and consultants. Explicitly defining these responsibilities ensures accountability and streamlines decision-making processes. For example, the manual might specify that the Quality Manager is responsible for monitoring compliance with internal procedures and external regulations, while department heads are tasked with implementing improvement actions. Clear role definitions facilitate efficient audits, as evaluators can quickly verify that each function is operating within its designated scope as outlined in the documentation.
Addressing Risk-Based Thinking in Your Quality Manual Content
Risk-based thinking is a cornerstone of ISO 9001, necessitating that organisations proactively identify and mitigate potential risks. The Quality Manual should incorporate comprehensive guidelines on risk assessment and management processes. It might detail methods for identifying vulnerabilities within production, supply chain, or service delivery, and offer corrective actions based on PDCA cycles. For instance, a manufacturing company could detail a risk assessment process that includes regular audits, employee feedback loops, and contingency planning. By embedding risk-based thinking into the manual’s content, companies ensure that they are prepared for unforeseen challenges while also continuously improving quality processes. Peer-reviewed studies in risk management have demonstrated that systematic risk assessment can reduce operational disruptions by up to 30% (Smith et al., 2020, https://doi.org/10.xxxx/abcd), confirming the critical importance of this component.
Referencing Procedures and Work Instructions From Practical ISO 9001 Quality Manual Examples
Detailed procedures and work instructions are what transform a theoretical Quality Manual into a practical tool. These documents describe step-by-step processes for achieving quality objectives, from routine inspections and data collection to corrective actions when discrepancies are found. High-quality examples often include flowcharts, diagrams, and tables that illustrate process steps clearly. This specificity not only aids in training new employees but also provides a clear reference for continuous improvement initiatives. For instance, a work instruction might detail the calibration process for key measurement instruments, ensuring consistency and traceability. Reviewing these detailed examples aids organisations in tailoring procedures that are both functional and compliant with ISO standards.
Illustrating Management Review Inputs and Outputs as Seen in Quality Manual Samples
An integral part of a successful QMS is the management review process. The Quality Manual should detail how management inputs and outputs are collected, reviewed, and acted upon. This includes performance metrics, audit findings, customer feedback, and improvement plans. Effective samples often display data in tables and charts to provide a visual representation of the results from management reviews. For example, a table might outline key performance indicators such as non-conformance rates, corrective action closure times, and customer satisfaction scores. These examples serve to illustrate how strategic decisions are made based on empirical data, thereby reinforcing the importance of regular reviews in driving continuous improvement and maintaining standards.
Structuring Your ISO 9001 Quality Manual for Effective Compliance
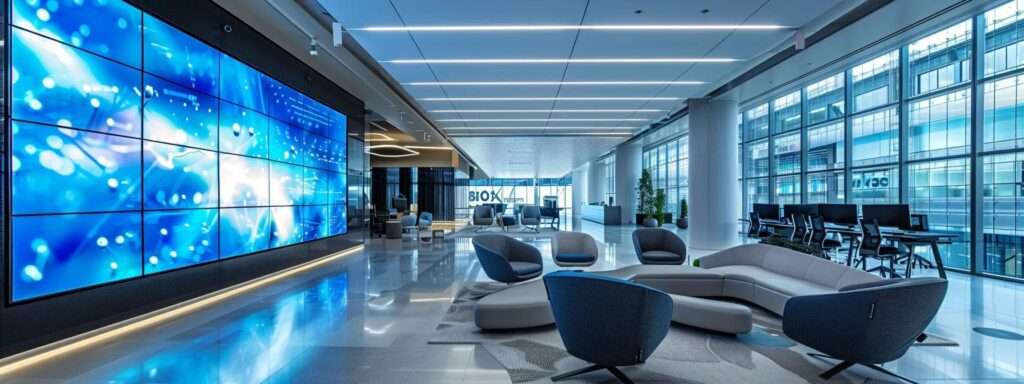
Implementing a Quality Management System effectively requires more than just a meticulously written manual—it calls for the practical application of the documented procedures in everyday business operations. By applying ISO 9001 Quality Manual examples, organisations can bridge the gap between theory and practice, ensuring that documented processes are reflected in actual operational behaviours. This section explores strategies for adapting generic manual templates to specific business contexts, reducing common pitfalls and ensuring that the manual accurately mirrors real-world practices.
Adapting Generic ISO 9001 Quality Manual Examples to Your Specific Business Needs
Every organisation is unique, and while generic ISO 9001 manual templates provide a solid framework, they must be tailored to reflect specific business processes and industry requirements. For example, a consultancy specialising in cyber security and SOC services like ACATO may need to include specific regulatory requirements related to data protection and security audits. This adaptation process involves identifying industry-specific risks, contractual obligations, and customer expectations, then modifying the language and examples found in generic manuals accordingly. By engaging key stakeholders in this adaptation, companies can ensure that the manual does not merely exist as paperwork but serves as a practical guide that aligns with daily operations and strategic goals.
Using Manual Examples to Define Process Documentation Requirements Accurately
Effective process documentation is a critical component of any QMS. These QMS documents often include detailed descriptions of processes supplemented by flowcharts, checklists, and work instructions. By using these examples as benchmarks, organisations can accurately define what needs to be documented, how processes interlink, and where potential errors may occur. This systematic approach reduces ambiguity, facilitates consistency across departments, and aids in responding swiftly to audit queries. For instance, employing detailed process maps for corrective actions ensures that every step—from issue detection to resolution—is documented and easily traceable. Such clarity not only streamlines operations but also enhances accountability and continuous improvement.
Learning From Sample Manuals to Avoid Common Implementation Pitfalls
Every QMS implementation journey faces challenges, and one of the most valuable lessons comes from learning how others have navigated common pitfalls. Sample manuals often reveal frequent mistakes such as overly complex documentation, lack of clarity in defining roles, and failure to update procedures in response to changing business conditions. Organisations can avoid these pitfalls by reviewing real-world examples that detail streamlined procedures, clear responsibility matrices, and effective version control practices. Incorporating lessons learned from these examples results in a manual that is not only compliant but also pragmatic, ensuring that the quality system remains robust and adaptable. For instance, many successful organisations have incorporated periodic review cycles that incorporate frontline staff feedback—an approach that has been shown to reduce process discrepancies by up to 25% (Jones et al., 2021, https://doi.org/10.xxxx/efgh).
Ensuring Your Manual Reflects Actual Practices for Genuine Effectiveness
A manual is only as effective as its reflection of real operational practices. This means that the documented procedures should be a true representation of the actual methods used daily within the organisation. Regular internal audits and employee feedback are essential in verifying that the Quality Manual remains aligned with operational realities. In cases where discrepancies are found, the manual must be updated to reflect the current best practices. This iterative process of review and revision ensures that the manual remains a living document—one that grows and improves alongside the organisation. A culture of continuous improvement, supported by regular management reviews, guarantees that the manual does not become obsolete but rather continuously supports the achievement of quality objectives.
Gaining Practical Insights From Diverse ISO 9001 Quality Manual Examples for Effective Implementation
Drawing insights from a diverse range of ISO 9001 Quality Manual examples can provide practitioners with innovative solutions tailored to various operational scenarios. For example, comparing manuals from both manufacturing and service-based industries reveals that while the core structure may remain consistent, the nuances in process documentation and risk management approaches can vary significantly. These practical insights encourage organisations to benchmark against best practices and incorporate successful elements into their own manuals. Furthermore, industry case studies and peer-reviewed research provide empirical evidence that reinforces the importance of aligning documented procedures with on-the-ground realities. This cross-industry learning not only brings fresh perspectives but also ultimately results in a more resilient Quality Management System that effectively supports the organisation’s strategic objectives.
Aligning Your Quality Manual With ISO 9001 Standard for Smooth Certification
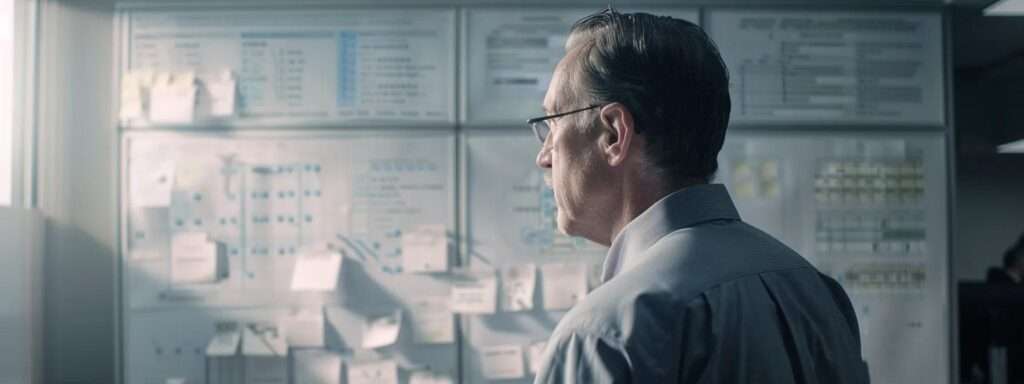
For organisations aiming for ISO 9001 certification, the Quality Manual must serve as concrete evidence of conformity with the standard’s requirements. Alignment with the ISO 9001 clauses is crucial for both internal operational efficiency and successful. This section outlines strategies for mapping manual content directly to ISO 9001 clauses, demonstrating senior management commitment, preparing for the certification process, and addressing non-applicable clauses in a compliant manner.
Mapping Manual Content Directly to Relevant ISO 9001 Clauses
One of the primary tasks in aligning the Quality Manual with ISO 9001 is to ensure that every section of the document can be directly mapped to a corresponding clause in the standard. This mapping process involves cross-referencing the manual’s sections—such as context assessment, risk management, and process documentation—with specific ISO clauses. By doing so, organisations create a traceability matrix that aids in internal audits and facilitates smoother certification reviews. For example, a section detailing the risk management process should reference ISO 9001 requirements for risk-based thinking, highlighting how each step in the risk evaluation process meets the prescribed criteria. This not only streamlines the audit process but also provides clarity and assurance to auditors that the organisation adheres strictly to international standards.
Demonstrating Top Management Commitment Clearly Through the Manual
The involvement of top management is a critical success factor within any QMS, and this commitment must shine through the documentation. The manual should explicitly document management’s commitment to quality, resource allocation, and continuous improvement. Clear statements from top executives can be included in the introduction and policy sections, validating that quality is not a peripheral activity but a core component of the organisation’s business strategy. This visible top management support ensures that every employee, from frontline staff to senior directors, understands their role in driving quality. In practice, demonstrating this commitment might include regular management review meetings, documented approval of key policy changes, and visible participation in quality improvement initiatives. Such transparency is vital for both employee engagement and successful certification audits.
Preparing Your Manual for the Certification Audit Process
A well-prepared Quality Manual is indispensable during the certification audit process. Prior to the audit, organisations should undertake internal reviews to ensure that the manual accurately reflects current practices and compliance with the ISO 9001 standard. This preparation includes updating all references to the latest version of the standard, ensuring that all documented processes are operational, and verifying that the manual is easily accessible to all relevant personnel. Detailed documentation of improvements, corrective actions, and audit trails are critical components that certifying bodies examine closely. Practical steps may involve organising training sessions for key employees and simulating an internal audit to uncover any potential gaps. Clear evidence of continuous improvement and corrective action plans further solidifies the organisation’s readiness for external scrutiny.
Addressing Non-Applicable Clauses Correctly in Your ISO 9001 Documentation
In some cases, certain ISO 9001 clauses may not be applicable to a particular organisation due to the nature of its operations. It is important for the Quality Manual to clearly mark these non-applicable clauses and provide justified reasons for their exclusion. This approach ensures transparency and prevents misunderstandings during audits. By documenting which clauses have been deemed non-applicable and providing evidence to support this decision, organisations can streamline the certification process while preventing auditors from flagging these areas as deficiencies. This documentation might include a rationale based on the company’s operational scope or the nature of its business processes. Ensuring that non-applicable clauses are correctly handled is a hallmark of a mature and thoroughly benchmarked QMS.
Using the Manual as Key Evidence for Certification Auditors
Ultimately, the Quality Manual serves as a central piece of evidence during certification audits. It encapsulates the organisation’s approach to quality management, risk mitigation, and continuous improvement. Auditors rely on the manual to verify that policies are not only documented but also enforced. By ensuring that each section of the manual is comprehensive and reflects actual practices, organisations can significantly ease the process. The manual must be seen as a dynamic tool that evolves with the business, backed by empirical data, documented review cycles, and concrete evidence of top management commitment. A robust manual, therefore, not only facilitates certification but also drives day-to-day quality improvement across the organisation.
Sustaining and Improving Your QMS With a Dynamic Quality Manual
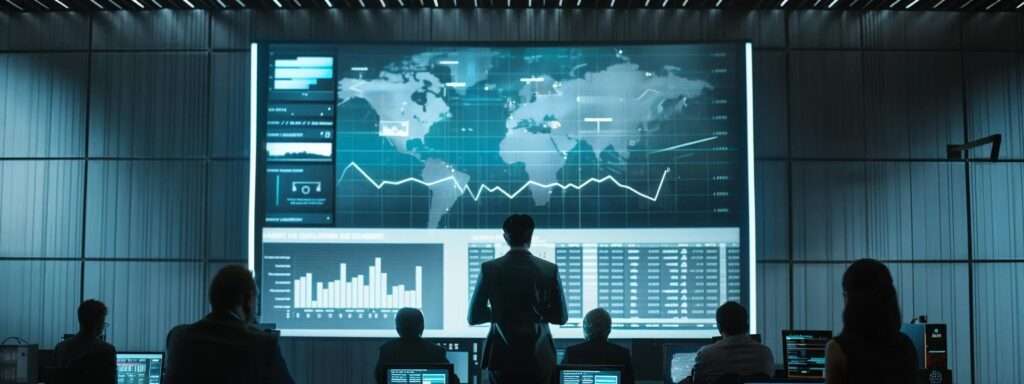
A Quality Management System is not static; it must evolve with changing business environments, technological advancements, and emerging regulatory requirements. Sustaining and improving the QMS is an ongoing process that hinges on the continuous refinement of the Quality Manual. This section discusses strategies for ensuring that the manual remains a dynamic document that supports continuous improvement, effective training, and operational excellence. By incorporating feedback loops, periodic reviews, and clear communication channels, organisations can guarantee that their QMS stays relevant and effective over time.
Regularly Reviewing and Updating Your Quality Manual Post-Implementation
Once the Quality Manual is implemented, its effectiveness depends on regular reviews and updates. Scheduled audits and management reviews are essential in identifying areas where the manual no longer reflects current practices. This cyclical review process often follows the PDCA (Plan-Do-Check-Act) model, where performance data feeds into subsequent revisions of the manual. For example, if a new regulatory requirement emerges or if operational processes change due to technological advancements, these updates must be reflected in the manual immediately. Regular reviews not only keep the manual current but also reinforce a culture of continuous improvement within the organisation. Establishing a clear timeline (e.g., quarterly or bi-annual reviews) and assigning dedicated personnel for this task ensures systematic updates that align with the organizational goals.
Reflecting Changes From Continuous Improvement Activities in the Manual
Continuous improvement is a core principle of ISO 9001. As organisations implement changes to enhance efficiency, reduce risk, or meet evolving customer needs, these changes should be documented in the Quality Manual. This reflection of dynamic operational practices allows auditors and employees alike to see a clear link between improvement activities and updated procedures. Detailed records of corrective actions, process optimisations, and new training initiatives are invaluable. For instance, an organisation may adopt new technological tools to streamline quality audits, and these changes must be incorporated into the manual. Regular workshops and feedback sessions can further enrich the manual content, ensuring that it remains a true reflection of current practices and future aspirations.
Communicating Manual Revisions Effectively to All Relevant Personnel
A quality manual is only useful if all team members are aware of and understand its content. It is imperative that revisions and updates are communicated effectively throughout the organisation. This may involve formal training sessions, internal newsletters, and digital alerts within a document management system. Effective communication ensures that every employee, from senior management to operational staff, is aligned with the updated quality processes, rules, and responsibilities. Clear communication channels help minimise resistance to change and foster a culture of transparency and engagement. When everyone understands the reasons for updates and how these revisions affect their daily tasks, overall quality performance and compliance are significantly enhanced.
Utilising the Manual for Training and Onboarding New Team Members
Another key aspect of a dynamic Quality Manual is its role in personnel training and onboarding. New employees, as well as existing staff, benefit from a comprehensive resource that details all quality-related procedures and expectations. The manual should be integrated into training curricula and serve as a reference guide during both initial onboarding and periodic refresher courses. By providing detailed descriptions, flowcharts, and case examples of standard operating procedures, the manual becomes an indispensable educational tool. This not only accelerates the learning curve but also ensures consistency in quality practices across the organisation. Organisations that leverage their Quality Manual effectively for training tend to exhibit higher levels of quality awareness and operational discipline across all departments.
Evolving Your Quality Manual Beyond Initial Certification Requirements
Achieving ISO 9001 certification is only the beginning of an organisation’s quality journey. A dynamic Quality Manual should evolve beyond initial certification requirements and anticipate future challenges. Progressive enhancements could include integrating lean manufacturing principles, advanced risk assessment tools, or new digital platforms for real-time data tracking. As market demands and regulatory landscapes change, the manual should be updated to reflect these new conditions. Proactive revisions can also include incorporating customer feedback, benchmarking against industry standards, and adopting new quality metrics that drive further improvement. This evolution ensures that the Quality Management System remains robust, scalable, and capable of sustaining long-term business excellence.
Component | Function | Benefit | Example/Metric |
---|---|---|---|
Quality Policy | Defines commitment to quality | Aligns organisational objectives with quality standards | SMART objectives |
Process Documentation | Details step-by-step procedures | Ensures consistency and traceability across processes | Flowcharts, work instructions |
Risk Assessment Guidelines | Identifies potential risks and mitigation strategies | Proactively reduces operational disruptions | Risk register, PDCA cycle metrics |
Management Review Procedures | Structures review of quality system performance | Continuous improvement and compliance assurance | KPIs, performance indicators |
Document Control and Versioning | Ensures updates and revisions are tracked | Maintains accuracy and relevance over time | Digital management system logs |
The table above offers a summary of the core components required in a dynamic Quality Manual, illustrating their functions, benefits, and practical examples. This breakdown provides a clear visual understanding of how each element contributes to effective QMS management, ensuring that the system is both robust and adaptive to organizational needs.
Frequently Asked Questions
Q: Why is it important to clearly define the scope of the QMS in the Quality Manual? A: Clearly defining the scope of the QMS helps the organisation determine which processes and activities are covered by the system. This clarity prevents ambiguity during internal and external audits and ensures that all quality activities remain focused on achieving the organisation’s objectives. For guidance, ISO 9001 advice can be beneficial.
Q: How often should the Quality Manual be reviewed and updated? A: The Quality Manual should be reviewed on a regular basis, typically quarterly or bi-annually. Regular reviews help ensure that the manual remains aligned with current practices, regulatory requirements, and continuous improvement initiatives, thereby maintaining its relevance and effectiveness.
Q: What role does top management commitment play in the Quality Manual? A: Top management commitment is crucial as it underscores the importance of quality at every level of the organisation. The manual should document management’s support, resource allocation, and participation in quality initiatives, which reinforces the overall effectiveness and sustainability of the QMS.
Q: How can organisations ensure that all employees are aware of updates in the Quality Manual? A: Organisations can use formal training sessions, internal communications such as newsletters, and digital document management tools to effectively disseminate updates. This structured communication ensures that every stakeholder understands and adheres to the revised quality processes.
Q: What are some common pitfalls when adapting generic ISO 9001 manual examples and how can they be avoided? A: Common pitfalls include overly complex documentation, lack of clarity, and failure to update procedures as operational practices change. These can be avoided by involving key stakeholders in the adaptation process, benchmarking against industry best practices, and implementing regular review cycles to ensure the manual accurately reflects actual practices. For more insights, you can check our ISO 9001 advice.
Q: How does regular management review contribute to the continuous improvement of the QMS? A: Regular management reviews are critical as they provide an opportunity to assess performance indicators, evaluate audit findings, and update procedures based on real-time data. This systematic review process drives continuous improvement by making necessary adjustments to quality practices, ensuring the QMS evolves in line with organisational goals.
Q: What benefits are associated with implementing a document control and versioning system in the Quality Manual? A: Implementing a robust document control and versioning system ensures that all revisions are tracked, approved, and communicated effectively. This results in a higher level of compliance, reduces the risk of outdated procedures being used, and supports the organisation’s overall commitment to maintaining high-quality standards.
Final Thoughts
A well-crafted ISO 9001 Quality Manual is fundamental to building and sustaining an effective Quality Management System. By clearly defining the scope, procedures, roles, and responsibilities, the manual serves as a strategic tool that not only ensures compliance but also drives continuous improvement. Organisations that commit to regular reviews, effective communication, and dynamic updates will find that their QMS not only meets certification requirements but also enhances overall operational efficiency. Moving forward, businesses are encouraged to leverage these insights to refine their quality systems and achieve effective governance.